Welcome to our guide on manufacturing orders. Whether you’re a seasoned business owner or just starting, understanding how manufacturing orders work is crucial for streamlining your production process and meeting customer demands efficiently.
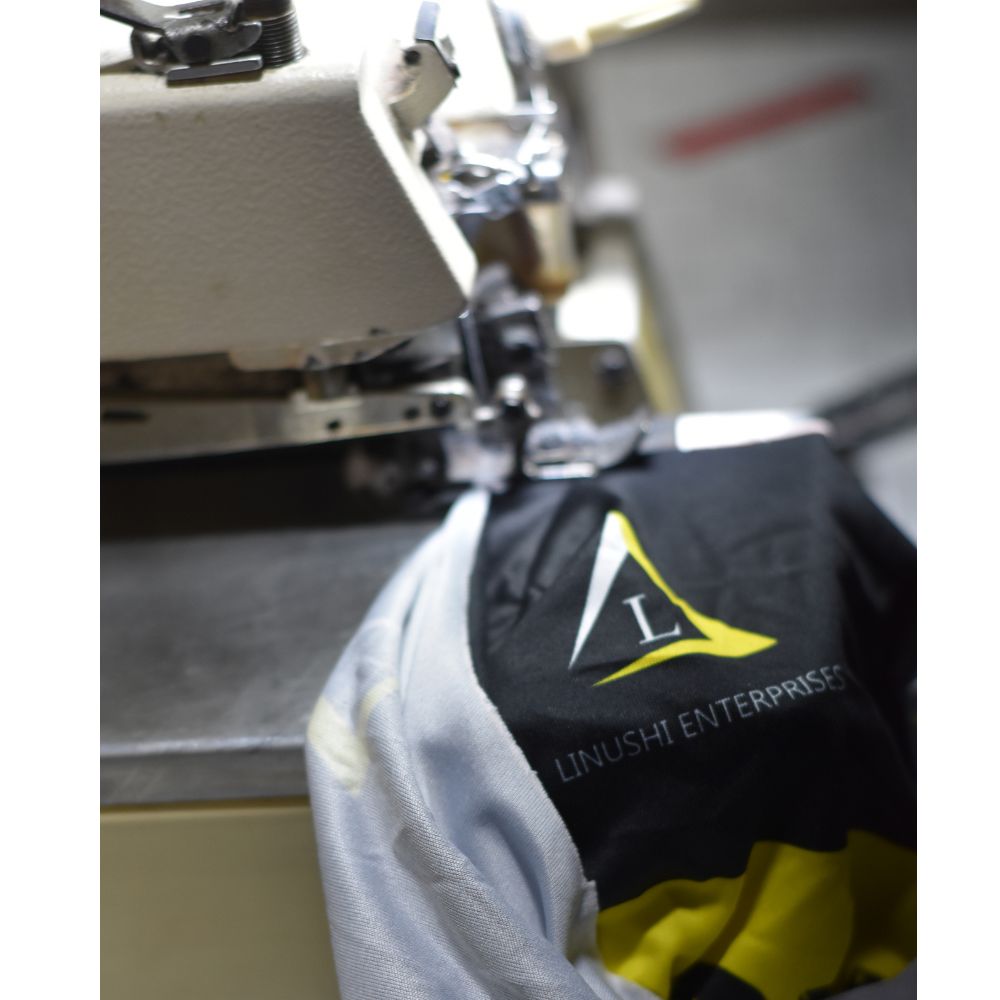
Key Components of a Manufacturing Order:
- Order information (customer name, order number, date)
- Product specifications (quantity, size, color, design)
- Production instructions (materials needed, deadlines)
- Quality control measures
- Shipping and delivery information
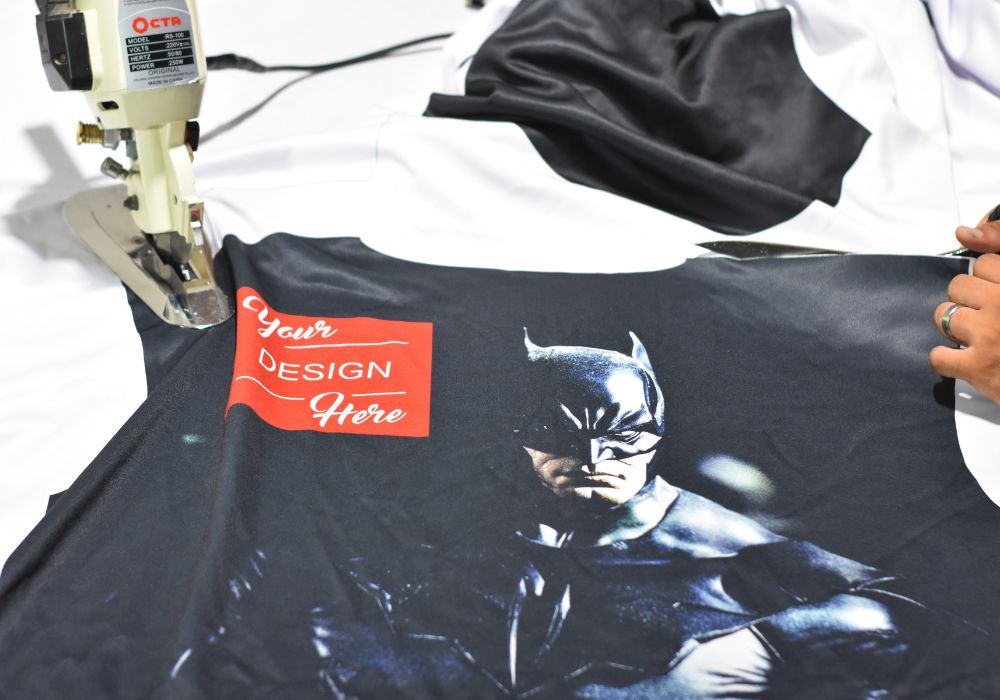
Price Points:
Our pricing depends on various factors such as quantity, style, customization options, and printing method. To give you an accurate quote, please provide more details such as:
- The type of Item you’re interested in (e.g., item style, item material)
- Any specific customization options (e.g., logo size, printing method)
- Desired colors
- Total Order quantity(Must one)
After knowing the above details, we will be able to provide you with a quote with rates.
What do we need from you to start the order?
To start an order you need to provide the following information
If you provide us with a tack pack, then that would be great; otherwise, just let us know the below details and we will make an order PDF for you.
The Manufacturing Process
Receiving the order
Once an order is placed, it’s logged into our system for processing.
Material procurement:
We ensure we have all necessary materials in stock or procure them from trusted suppliers.
Production or assembly:
Skilled workers handle the production or assembly of the products according to the specifications provided.
Quality assurance:
Each product undergoes thorough quality checks to ensure it meets our standards before proceeding to the next step.
Packaging:
Products are carefully packaged to prevent damage during shipping.
Shipping
Orders are dispatched for delivery to the customer’s specified location.